NETSTAL has launched a new option for hybrid injection moulding machines - adaptive system pressure reduction can permanently determine the optimum operating pressure in the hydraulic system.
In order to handle peak loads without any problems, the hydraulic system of hybrid NETSTAL injection moulding machines is designed for a maximum operating pressure of 250 bar. RUBBER MOULD
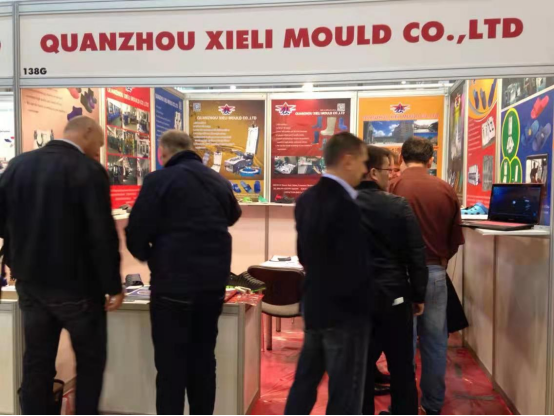
"This is where we come in with the new system pressure reduction and make our machines even more energy efficient. In automatic mode, the adaptive control system determines the optimum point at any time and adjusts the system pressure accordingly. With the same or even increased productivity, the energy consumption for providing the system pressure is reduced to a minimum," explains Daniel Wipfli, product manager at NETSTAL.
Smaller carbon footprint and higher cash flow
In addition, NETSTAL claims there are further ecological and economic advantages for customers. The lower energy consumption of the machine also reduces the user's ecological footprint. Depending on the regional electricity mix, less CO2 is emitted.
In most cases, the small surcharge for adaptive system pressure reduction pays for itself within a few months. The payback period varies depending on the region and electricity costs. In some countries, investments in more energy-efficient and climate-friendly production facilities are subsidised with government grants.
"For customers, we are happy to calculate the individual savings potential and show how they can manufacture identical products at a lower cost and with a smaller CO2 footprint," says Wipfli.
Part of Rapid News Group

Pvc Airblowing Slipper Mould © Rapid Med-Tech Communications Ltd. A Rapid News Group Company. All Rights Reserved.